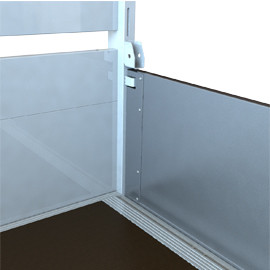
FRONT FACE WELDED TO THE PLATFORM
The front face welded to the platform provides the strength for the bodywork.
The front face welded to the platform provides the strength for the bodywork.
The rigidity of the anodised aluminium sideboard is provided by its boxing.
The most robust welding technique on the market.
0.5 l/100 km fuel savings with JPM aluminium bodywork (compared with its steel equivalent).
Over the last 10 years the JPM fleet in circulation in Europe represents 20,000 aluminium bodies.
65 kg of additional payload for a 3300 mm JPM aluminium dropside/wood platform compared with its steel equivalent.
All JPM tippers are fitted with stops on which the sideboards and the door rest when they are open.
Lashing on the platform is possible using the return on the outer frame.
The net can be easily fixed to the sideboard.
Customise your JPM tipper very simply: order options via our store and fit them easily and quickly. In this way you have a tipper customised to your professional requirements. In spite of everything, this same tipper can evolve. It can be customised in a different way at any time.
Collision or an unfortunate impact with a bucket can happen quickly on a site. Carry out repairs yourself in record time: order your door or your sideboards with just a few clicks on the JPM website.
2 years’ guarantee on purchase of the tipper
+ 1 additional year free when registering the tipper guarantee on our website
+ 2 additional years on sale on our website
FINISH
Anodised aluminium sideboards
Aluminium elements:
Shot blasting + 60 µm powder primer + 60 µm powder paint